First. Process flow diagram of AAC block production line
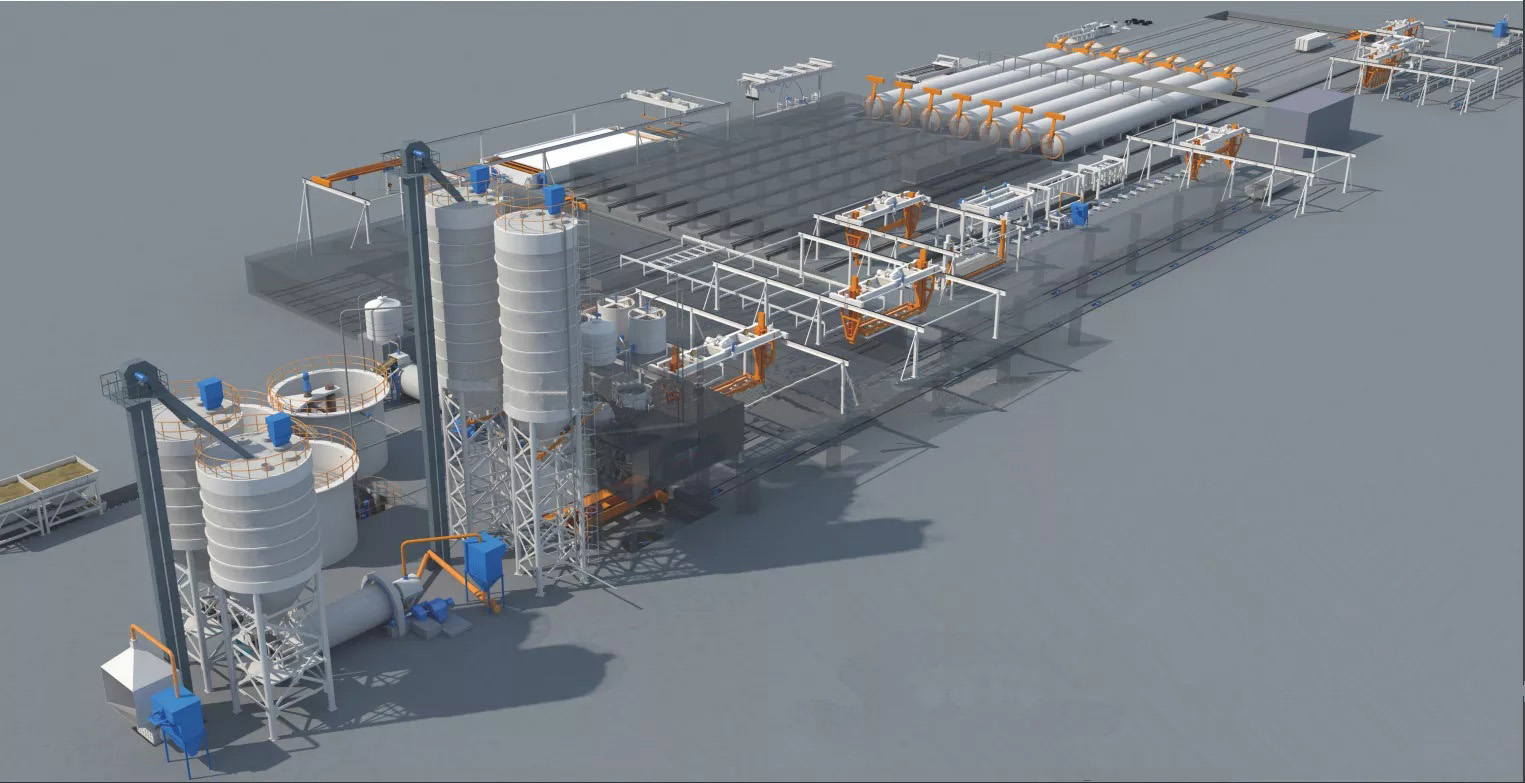
1. Raw materials processing
Put the fly ash or sand into the ball mill to mill via the conveyor belt, after milling, put the slurry into the slurry storage tank by slurry pump.
2. Batching, mixing and casting
The lime, cement will convey by conveyor to the dry powder measure scale to scale separately. The slurry convey by slurry pump then to the automatic scale;the power and slurry put into the mixer,pouring into the mould.
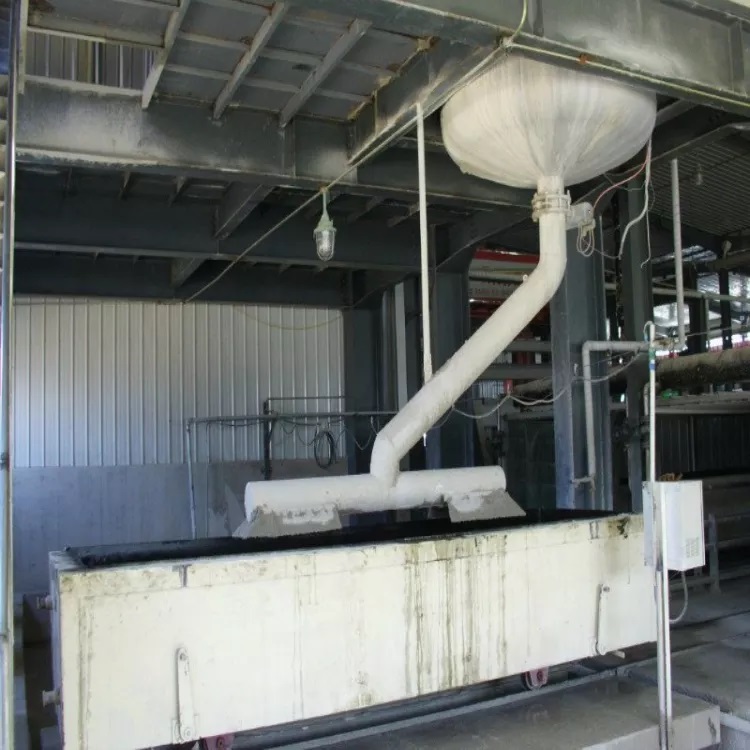
3. Curing
After slurry pouring into the mould, put the mould box into the curing room with 50~70℃. After 2-3 hours curing,the blocks become solid.
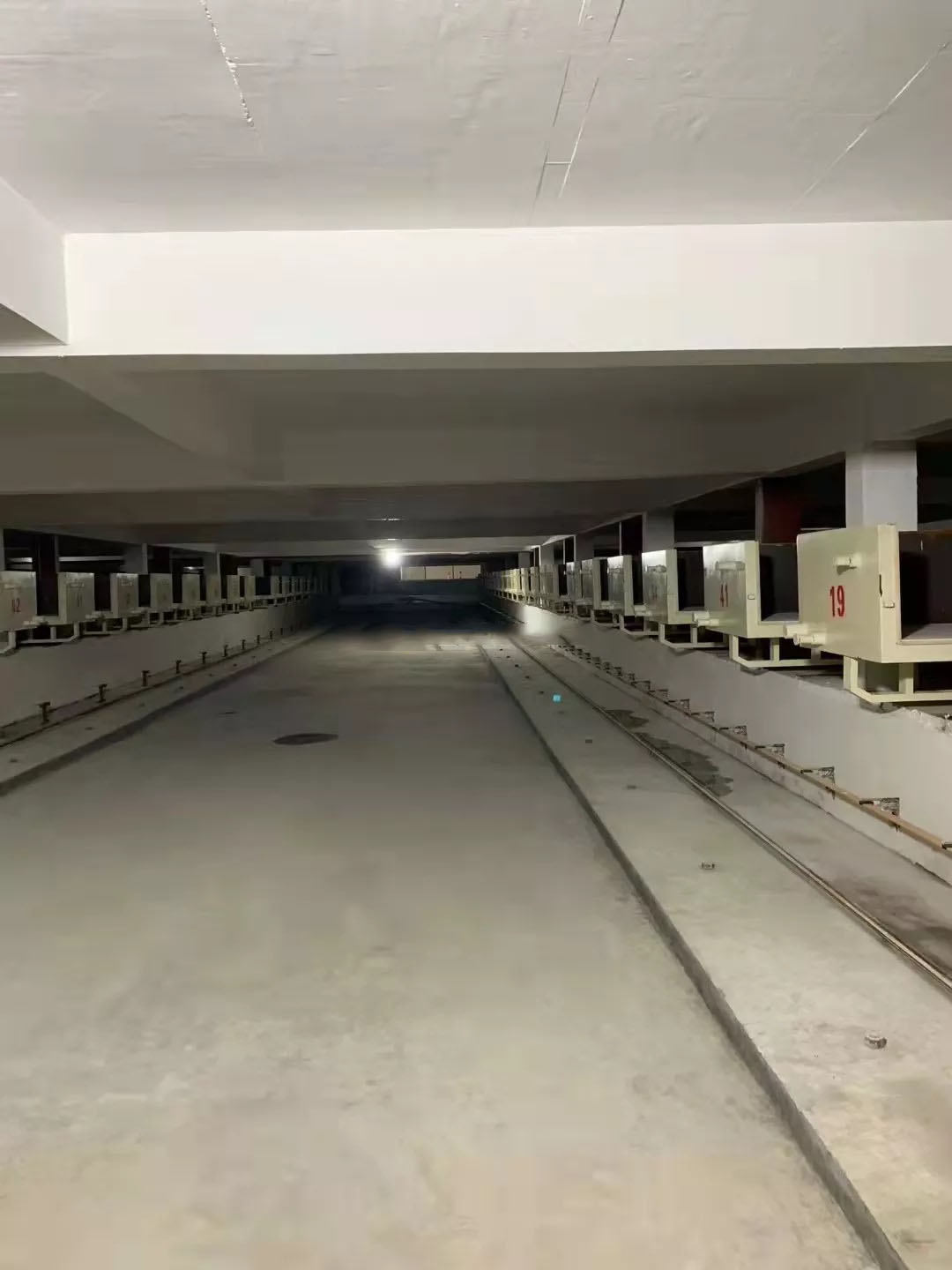
4. Cutting
Using reversal crane carry the mould and block to demould on cutting cart. The cutting cart will take the block to level cutting machine,vertical cutting ,two sides cutting,and remove the top waste material.
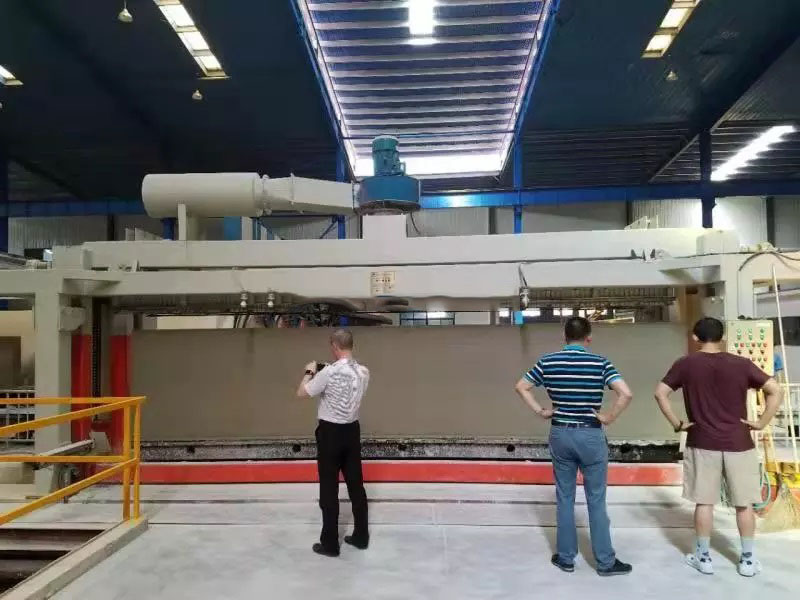
5. Steaming
Finished cutting using semi-product crane carry to the front of autoclavegrouped,hoisting machine or dragger will drag steam trolley into autoclave to steam,it need 10-12 hours.

6. Finished block dealing
Finished product out of autoclave,with separting machine to separate layer by layer.
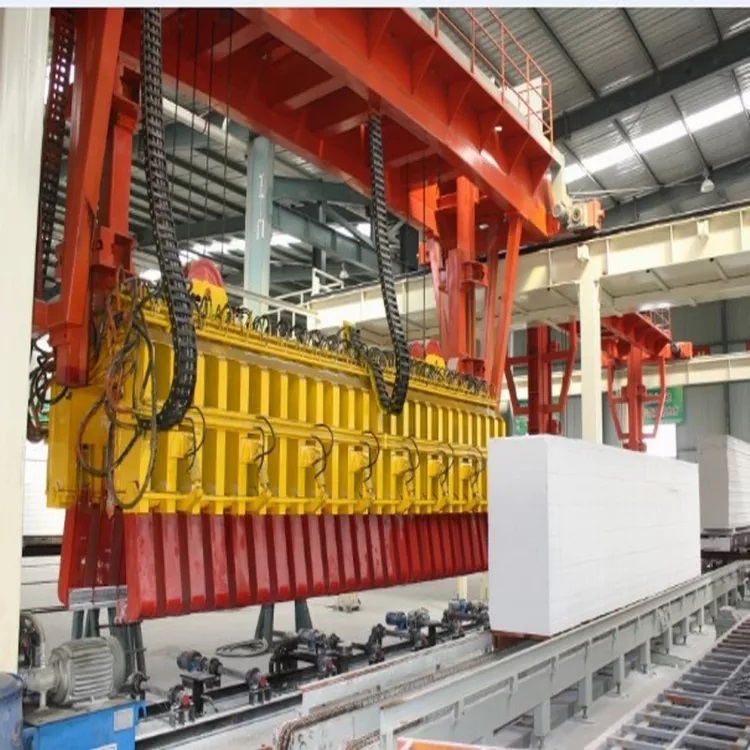
7. Packing
Using finished block carry hanger clamp the finished product to package line on wooden pallets,after package, then by forklift transport the finished products to piled yard according to specifications to stack.
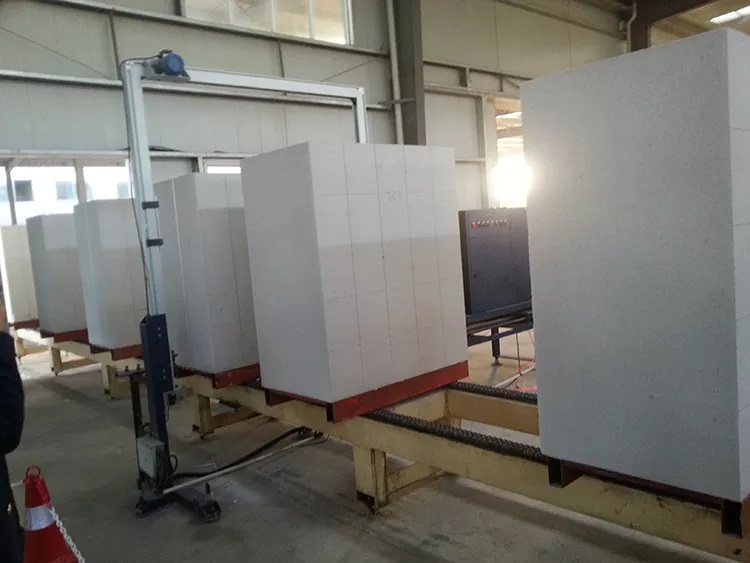
Second. Raw material proportion of AAC block production line
1. Fly ash type
Name | Unit | Proportion |
Fly ash | % | 65-70 |
Cement | % | 6-15 |
Lime | % | 18-25 |
Gypsum | % | 3-5 |
Aluminum powder paste (600kg/m³) | 1/10000 | 8 |
Water & material rate |
| 0.60-0.65 |
Curing temperature | ℃ | 36-40 |
Aluminum mixing time | S | 30-40 |
2. Sand type
Name | Unit | Proportion |
Sand | % | 55-65 |
Cement | % | 10-20 |
Lime | % | 20-30 |
Gypsum | % | 2-3 |
Aluminum powder paste (600kg/m³) | 1/10000 | 8 |
Water & material rate |
| 0.65-0.75 |
Curing temperature | ℃ | 35-38 |
Aluminum mixing time | S | 30-40 |
Third. Packing and delivery of AAC block production line
1. General AAC block plant equipment transport with 40 HQ container.
2. Ball mill transport with 40 OT or 40 FR according the size.
3. Autoclave transport on deck of ship.
4. Cutting machine usually transport with 40 FR or on deck of ship.
Welceom to contact us for details.